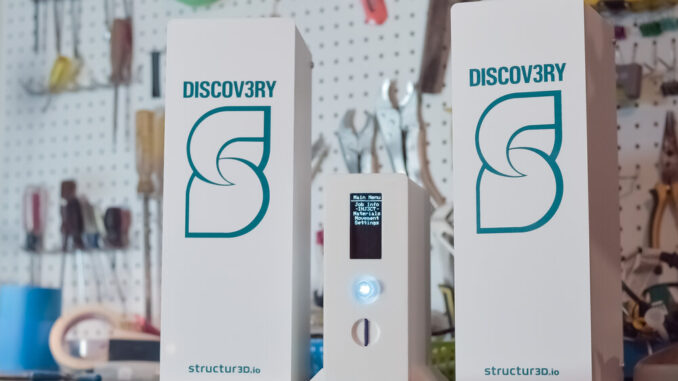
Kanadyjska firma Structur3d przedstawiła nowe rozwiązanie do tworzenia prototypów i niskoseryjnej produkcji części gumowych poprzez połączenie druku 3D i formowania wtryskowego. Wszystko… na biurku!
Platforma Inj3ctor jest prawdopodobnie pierwszą na rynku w segmencie małych (biurowych) urządzeń do rapid prototyping, która pozwala na uzyskanie elementów gumowych o parametrach porównywalnych do tych pochodzącej z seryjnej produkcji.
– Jako zespół naukowców i inżynierów chemików […] rozszerzyliśmy możliwości materiałowe drukarek 3D poza standardowe tworzywa sztuczne – powiedział Charles Mire, dyrektor generalny i współzałożyciel Structur3d.
Elementy gumowe w druku 3D
Materiały gumopodobne są pożądane ze względu na swą elastyczność, ale ich wytrzymałość (kruchość) uzyskana w procesie druku 3D często ogranicza ich zastosowanie w częściach funkcjonalnych. Obecnie elastomery są w tym segmencie używane głównie jako żywice, ale ostatnio opracowano kilka nowych materiałów. Jakich?
W czerwcu br. amerykańska firma 3D Systems wprowadziła na rynek swój elastomer Figure 4 RUBBER-65A BLK, który wykazywał wysoką wytrzymałość na zerwanie, zapewniając elastyczność i trwałość, dzięki czemu doskonale nadaje się do stosowania w uszczelkach powietrznych, przeciwpyłowych oraz uszczelnieniach w elektronice.
W tzw. międzyczasie firma Fillamentum Industrial także wprowadziła szerszy wybór materiałów, w tym elastyczną żywicę elastomerową Flexfill TPE, odpowiednią do prototypowania, zwłaszcza do produktów medycznych (elastycznych elementów takich jak uszczelki).
Kolejna amerykańska firma Adaptive3D we współpracy z holenderską DSM skomercjalizowała miękki gumopodobny materiał na bazie żywicy, który będzie sprzedawany pod nazwą Soft ToughRubber. Wcześniej samodzielnie wprowadziła odporny na naprężenia fotopolimer Damping ToughRubber.
Niedawno naukowcy z Virginia Tech University (VTU) Macromolecules Innovation Institute (MII) i Michelin North America stworzyli nowatorski drukowany w 3D gumowy materiał lateksowy, który może znaleźć zastosowanie w takich dziedzinach, jak robotyka, urządzenia medyczn, czy amortyzatory. W międzyczasie, kalifornijski dostawca usług szybkiego prototypowania, GoProto uruchomił nową usługę druku 3D o nazwie 3DElastroPrint, która specjalizuje się w wytwarzaniu „gumopodobnych” części na bazie elastycznego, lekkiego termoplastycznego poliamidu (TPA) produkowanego przez Evonik i zoptymalizowanego pod kątem technologii HP Multi Jet Fusion (MJF).
Inj3ctor
To rozwiązanie umożliwiające druk 3D i formowanie wtryskowe dosłownie „na biurku”, wykorzystuje przemysłowe, profesjonalne materiały, jak silikony i poliuretany. Platforma Inj3ctor wykorzystuje drukowane na drukarkach 3D formy do wtryskiwania dwuskładnikowych elastycznych materiałów.
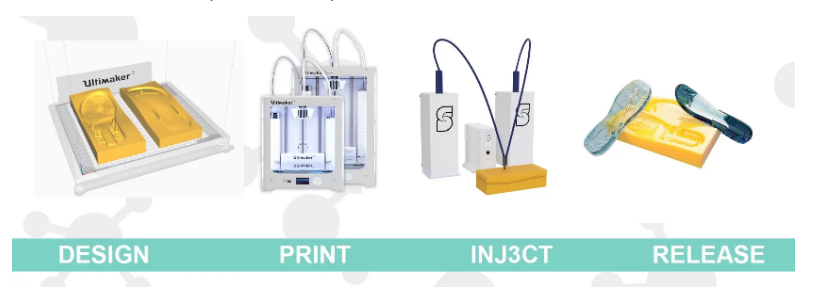
Niezbędna jest forma wydrukowana na drukarce 3D…
Projekt formy powstaje w systemie CAD, następnie jest drukowany przy użyciu standardowego, trwałego (lub rozpuszczalnego tworzywa) za pomocą drukarki 3D Ultimaker S5.
Użytkownicy mogą następnie zastosować setki, jeśli nie tysiące płynnych materiałów gumowych, aby osiągnąć pożądaną trwałość, elastyczność i właściwości utwardzania. Przy zachowaniu określonych proporcji mieszania składników i objętości drukowanego elementu, Inj3ctor wypełnia drukowaną formę 3D, tworząc elastyczną część. Proces ten udało się dobrze dostosować do produkcji małych partii – na żądanie (ang. on demand) – gumowych prototypów i części nadających się do użytku końcowego.
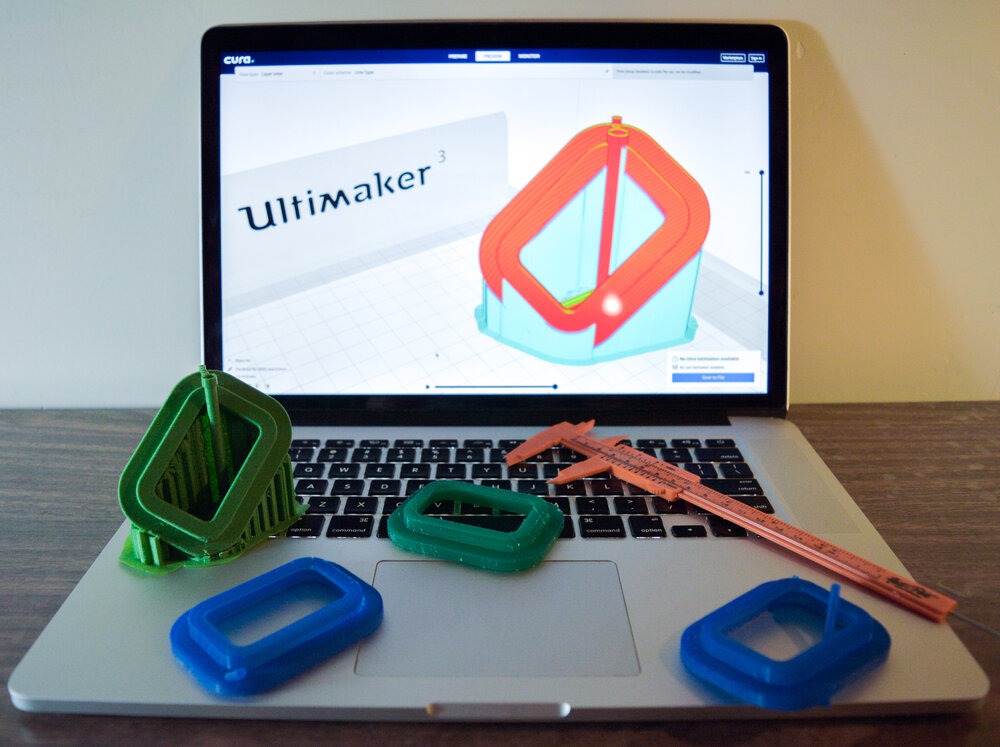
Według Structur3d metoda ta może być stosowana w wielu gałęziach przemysłu, w tym w motoryzacji, produktach przemysłowych, lotnictwie, energetyce, medycynie, czy różnych produktach konsumenckich. Platforma eliminuje kosztowne i czasochłonne etapy wytwarzania wyrobów gumowych. Ponieważ producenci coraz śmielej spoglądają w przyszłość niestandardowej produkcji na żądanie, Inj3ctor może otworzyć drzwi firmom myślącym poważnie o wdrożeniu technologii wytwarzania przyrostowego.

Pierwsza partia Structur3d Inj3ctor trafia właśnie do producentów. Pakiet platformy Inj3ctor obejmuje urządzenie Inj3ctor, drukarkę 3D Ultimaker S5, materiały towarzyszące i dodatkowe akcesoria.
Źródło: 3dprintingindustry.com, TenLinks.com
Bądź pierwszy, który skomentuje ten wpis