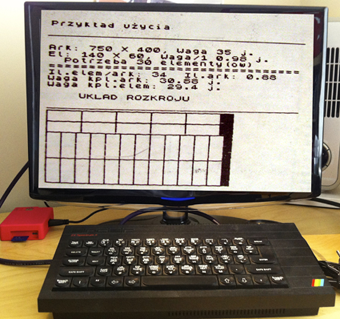
Do podjęcia tematu optymalizacji rozmieszczania wycinanych elementów na arkuszach blach zainspirował mnie artykuł Józefa Ludwińskiego, znaleziony w starym numerze czasopisma dla użytkowników mikrokomputerów…
Autor: Maciej Stanisławski
Na łamach „Bajtka” z 1989 roku*, miesięcznika, którego adresatami byli głównie posiadacze 8-bitowych komputerów, o pamięci operacyjnej w granicach 48-128 KB (!) – Józef Ludwiński zamieścił tzw. „listing” ** programu (vide rys. 1.), który miał za zadanie znaleźć optymalny sposób podziału dużego arkusza na jednakowe elementy mniejsze. Danymi wejściowymi, które wprowadzał użytkownik do pracującego już programu, były: wymiary arkusza, wymiary elementu i zapotrzebowanie na ów element.
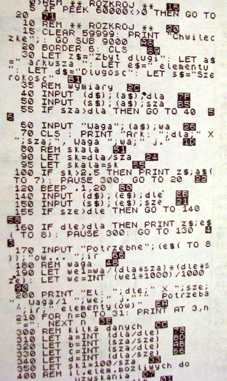
Wynikiem działania programu była:
1. wizualizacja – układ rozkroju (vide rys. 2.),
2. informacja na temat ilości arkuszy potrzebnych do realizacji zapotrzebowania,
3. wydajność z arkusza.
Dodatkowo, po podaniu masy surowca, obliczana była masa elementów oraz potrzebnych arkuszy.
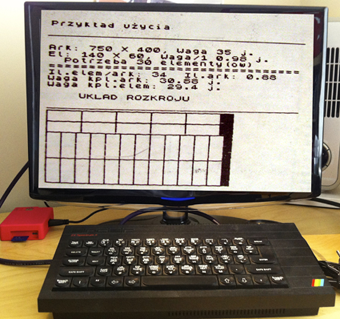
Autor programu zaznaczył, iż jest to tylko jeden z bardzo prostych przykładów na praktyczne wykorzystanie mikrokomputerów. Przykładów inspirujących, bo ewoluujących wraz z rozwojem sprzętu i systemów informatycznych. Swoją drogą, ciekawe, czy w 1989 roku w Polsce funkcjonowało już pojęcie „nestingu”?
Pod pojęciem tym kryje się taki sposób rozmieszczenia wycinanych płaskich elementów (np. na arkuszu blachy), aby zminimalizować straty materiału – odpady powstałe w procesie wycinania. Idealnym rozwiązaniem jest dodatkowo takie zagospodarowanie powierzchni, by część krawędzi sąsiadujących ze sobą elementów pokrywała się – żeby elementy te miały wspólne „linie cięcia”. W ten sposób producent może osiągnąć korzyści w dwóch obszarach.
Pierwszy to wspomniane już i oczywiste straty materiału. Niezależnie bowiem od tego, czy wycinamy jeden element, czy też kilkanaście, najczęściej dysponujemy określonym arkuszem blachy – standardowym, dostarczanym przez producenta, walcownię etc. Naturalnym jest zatem, że nawet jeśli zlecenie jest jednostkowe, to sprytne rozmieszczenie elementów nawet o różnych kształtach na jednym arkuszu materiału, przyniesie wymierne zyski – mniej odpadu.
Co więcej, optymalizacja rozmieszczenia elementów pozwala także na wybór możliwie małego arkusza blachy wystarczającego do realizacji zadania.
Drugi – to krótszy czas cięcia, przekładający się na większą szybkość realizacji zlecenia. Zgrupowanie elementów skraca czas potrzebny na przechodzenie głowicy tnącej między nimi. Uwspólnienie krawędzi oznacza, że jedno cięcie przypada na dwa elementy – skraca się przebieg maszyny.
Tak, czy inaczej, zastosowanie „nestingu” sprawia, że osiągamy wzrost wydajności przy jednoczesnej redukcji kosztów. Trudno zatem się dziwić, że do optymalizacji starano się zaprząc nawet takie maszyny, jak tytułowe ZX Spectrum. I w przypadku tego konkretnego programu na 8-bitowego „staruszka” zaryzykowałbym nawet stwierdzenie, że mamy do czynienia z „pierwocinami” systemu CAD, czy też czegoś z pogranicza CAD/CAM.
Obecnie bez większych problemów możemy znaleźć w Internecie (nierzadko darmowe – przyp. autora) programy, spełniające identyczne zadania – rozplanowują bowiem i analizują optymalną ilość elementów na danym obszarze, przy tym dysponują najczęściej możliwością importu płaskiego rysunku (rozkroju) zapisanego do formatu standardu DWG/DXF (vide rys. 3a i 3b).
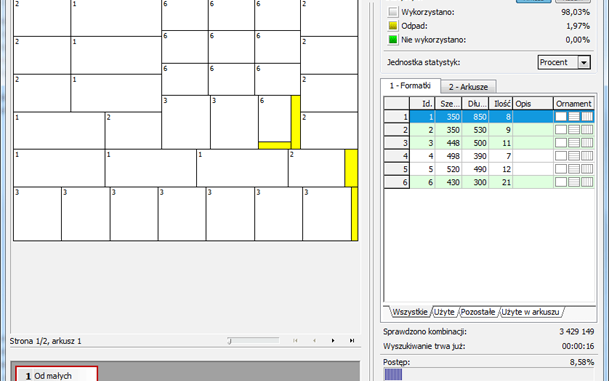
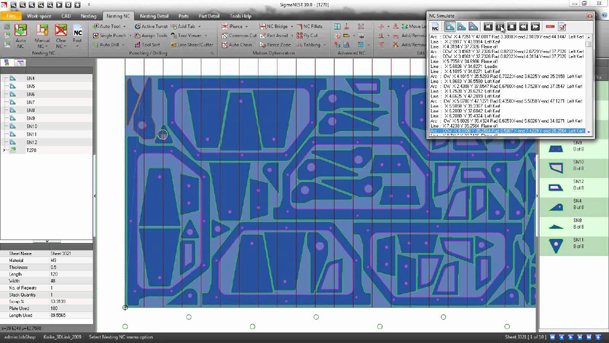
A przecież optymalizacja procesów związanych z wytwarzaniem elementów uzyskiwanych z arkusza blachy sięga znacznie dalej…
Gdy przyjrzymy się ofercie producentów systemów CAD/CAM zauważymy, iż na rynku obecnych jest wiele nakładek implementujących funkcjonalność „nestingu” do środowiska większych systemów. Nie oznacza to oczywiście, iż funkcjonalność taka nie jest obecna jako „standard” w profesjonalnych rozwiązaniach klasy np. NX CAM, ale dzięki nakładkom, rozmaitym „plug-inom” etc. staje się dostępna nie tylko dla posiadaczy… ZX Spectrum 48KB, ale także np. użytkowników bezpłatnego oprogramowania DraftSight.
Tymczasem można o wiele, wiele więcej. Dobry program do optymalizacji pracy z arkuszami blach integruje cały proces programowania CNC, od etapu projektowania w CAD 2D (lub 3D), przez wybór i definiowanie technologii cięcia/wykrawania, nakładanie na arkusz, aż po generowanie kodu NC i wysyłanie go do maszyny (rys. 4.).
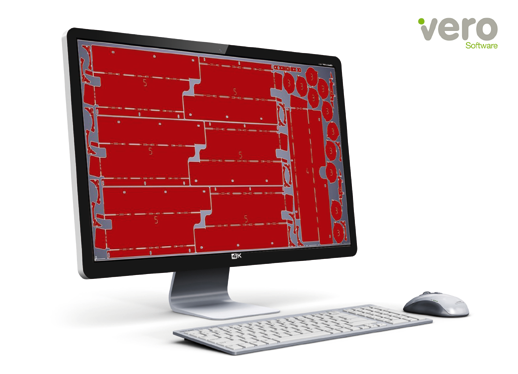
Rys. 4. Przykładem współczesnego, sprawdzonego programu do optymalizacji pracy związanej z wycinaniem elementów z arkuszy blach może być RADAN firmy Vero Software…
Trzeba także wziąć pod uwagę fakt, iż współczesne maszyny umożliwiają np. wykrawanie bardzo blisko łap, blisko krawędzi, używanie narzędzi takich jak: koła, przecinaki, nożyce oraz zmienne narzędzia znakujące. Dobry program powinien posiadać definicje/specyfikacje takich narzędzi i generować kod NC, który będzie mógł wykorzystać w pełni możliwości obrabiarki.
A jeśli chodzi o sam nesting, niezbędna wydaje się np. obsługa automatycznej wspólnej linii podczas wycinania – gwarantująca pełne wykorzystanie materiału, zapewniająca jednocześnie ograniczenie czasu wycinania i redukcję zużycia gazów. Części, które mogą być poddane wspólnej linii cięcia są grupowane razem tak, aby ograniczyć ryzyko uszkodzenia podczas wycinania dużej ilości detali…
(ms)
Źródło:
Józef Ludwiński: Rozkój. W „Bajtek”, nr 1/89, s. 13
http://www.radancnc.pl/wykrawanie-wycinanie/radcombi
https://optymalizacja-rozkroju.waw.pl/
Ciekawe linki
• Czytaj także o ZW Nesting – polskim rozwiązaniu dla ZWCAD
• Optymalizacja rozkroju w systemach CAD cz. II
Bądź pierwszy, który skomentuje ten wpis