  .png)
W przygotowaniu
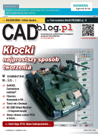
nr 5-6(25-26) 2017
dostępny
po 29.12.2017
Wydanie aktualne
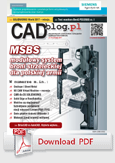
nr 3-4(23-24) 2017
dostępny w pdf, wydanie
flash
tutaj
Wydania
archiwalne
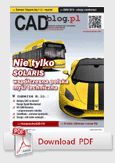
nr 1-2(21-22) 2017
dostępny w pdf, wydanie
flash
tutaj
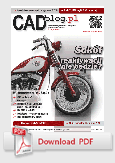
nr 1-2(19-20) 2015
dostępny w pdf, wydanie
flash
tutaj
2014_miniatur.png)
numer 1(18) 2014
dostępny w pdf, wydanie
flash
tutaj
2013_sm.png)
numer 1(17)
2013
dostępny w pdf, wydanie flash
tutaj
_covsmall.gif)
numer 1(16) 2012
dostępny
w
archiwum
2011_cover_small_ok.gif)
numer 1(15) 2011
dostępny
w
archiwum
cov_small.gif)
numer 4(14) 2010
HD dostępny
w archiwum
2010_cover_sma.gif)
numer 3(13) 2010
HD dostępny
w archiwum
2010small.gif)
numer 2(12) 2010
dostępny
w archiwum
2010_rgb_sm.gif)
numer 1(11) 2010 dostępny
w archiwum
2009_cover_web_small.jpg)
numer 9(10) 2009
już dostępny
w archiwum
_cover_web_small.jpg)
numer 8(9) 2009
już dostępny
w archiwum
2009_cover_small.jpg)
Wydanie specjalne
numer 7(8) 2009
już dostępny
w archiwum
_cover_web.gif)
Numer 6(7) 2009
już dostępny
w archiwum
|

Fragment artykułu z nr 1(11) 2010 (kompletne wydanie do pobrania z
Archiwum)
„Drukowanie” ...nożem? Przegląd współczesnych technologii
szybkiego prototypowania cz. I
Każda większa konferencja związana z systemami CAx stwarza
okazję do zapoznania się z metodami szybkiego prototypowania,
określanymi bardzo często mianem „druku 3D”. Większość
czytających te słowa zetknęła się już zapewne z prototypami
uzyskanymi na maszynach, których zasada działania zbliżona
jest często do zwykłych drukarek komputerowych. Nie da się
ukryć, iż technologie druku przyrostowego polegające na
budowie modelu z kolejno nanoszonych cieniutkich warstw
materiału zyskują coraz większą popularność. A jednak nie
wszystkie mają cechy łączące je ze wspomnianymi drukarkami...
AUTOR: Mateusz Bubicz
Dlatego jestem zdania, że jednak bardziej zasadnym wydaje się
używanie terminu „szybkie prototypowanie”, czy też ang. „rapid
prototyping”, niż ograniczanie się jedynie do zwrotu „druk
3D”, jak ma to miejsce niestety na okładce tego e-wydania.
Obejmuje ono bowiem jedynie niewielki wycinek wszystkich
dostępnych technologii budowania prototypów. Podejmując wątek
związany z „RP” (po z górą dwuletniej przerwie), od tego
właśnie chciałem rozpocząć cykl artykułów mających na celu
przybliżyć Państwu dorobek i nowości, z jakimi mamy do
czynienia w tej dziedzinie. A także – zastanowić się, na ile
uzasadnione w naszej sytuacji byłoby nabycie własnego
urządzenia do szybkiego prototypowania. Bo o tym, iż warto
korzystać z usług firm lub instytucji (np. uczelni
technicznych) posiadających takie maszyny, „drukarki 3D”,
również będę się starał Państwa przekonać. I nie dlatego, że
„ktoś mi za to płaci”. Zatem...
Dlaczego?
Duża
konferencja. Ponad pięć tysięcy zaproszonych użytkowników
systemów CAD. Wielka hala pawilonu wystawców, a pośród
prezentowanych technologii, urządzeń, oprogramowania, kilka –
jak zawsze w takich okolicznościach – stoisk przedstawicieli
firm produkujących maszyny do szybkiego prototypowania. Jak
wspomniałem, tematykę tą podejmowałem dwa lata temu i ciekaw
byłem, co też w tej dziedzinie dokonało się nowego. Pierwszy
wniosek, który nasuwa się niemalże od razu, to –
miniaturyzacja. Miniaturyzacja rozumiana w znaczeniu dążenia
do uczynienia urządzeń jak najbardziej kompaktowymi.
Jeszcze do niedawna „mała drukarka 3D” miała gabaryty
porównywalne ze sporej wielkości szafą, ewentualnie – z dużym
zestawem kserograficznym. W chwili obecnej w ofercie prawie
każdego producenta można znaleźć urządzenie, które nawet jeśli
nie zmieści się na biurku (a są już takie), to spokojnie
będzie się nadawało do ustawienia w kącie biurowego pokoju (hmm...
w redakcji CADblog.pl byłoby to jednak niemożliwe, gdyż w
kącie pokoju stoi rozgrzebany motocykl), a jego praca nie
będzie przeszkadzała osobom przebywającym w tym pomieszczeniu.
Maszyna będzie pracowała cicho, bezwonnie, nieuciążliwie dla
otoczenia. I doszukiwałbym się w tym kierunku zmierzającej
ewolucji już istniejących technologii szybkiego
prototypowania.
Siadam zatem do stanowiska CAD, do którego bezpośrednio lub
poprzez sieć podłączona jest „drukarka 3D”. Oprócz systemu CAD,
mam zainstalowane oprogramowanie (najczęściej dostarczone
razem z urządzeniem do prototypowania 3D), pozwalające na
wygenerowanie na podstawie mojego projektu danych zrozumiałych
dla maszyny; danych, które pozwolą na fizyczne uzyskanie tego,
co opracowałem w postaci cyfrowej, wirtualnej. I to „fizyczne”
nie będzie oznaczało płaskich wydruków dokumentacji
technicznej, pokrywających arkusze papieru, ale... model
wykonany z tworzywa, nierzadko funkcjonalny, pozwalający na
praktyczne sprawdzenie, jak będzie pasował i współpracował np.
z już istniejącymi komponentami modernizowanego urządzenia.
Jak najłatwiej sprawdzić ergonomię nowego telefonu
komórkowego? Uchwytu wiertarki udarowej? Obudowy szlifierki
kątowej? Narzędzia chirurgicznego? Biorąc je do własnej ręki.
To właśnie możliwe jest dzięki technologiom szybkiego
prototypowania. Kończymy cyfrowy projekt, zapisujemy go,
wysyłamy dane do maszyny, idziemy na kawę, zebranie,
sprawdzamy dokumentację i po kilku godzinach – jeszcze tego
samego dnia – mamy w rękach gotowy model fizyczny.
Udany? Doskonale! Nie udany? Nic nie szkodzi, naniesiemy
poprawki, kolejny „wydruk” ustawimy w kolejce i po przyjściu
do pracy rano znowu będziemy mogli obejrzeć nowy model. Bez
konieczności tworzenia kosztownych form. Bez ryzyka
uszkodzenia narzędzi obróbczych. A jeśli na przeszkodzie stoją
jednak finanse niezbędne do zakupu zarówno maszyny do
szybkiego prototypowania, jak i materiałów eksploatacyjnych i
obsługi serwisowej (tak, tak – opiekę serwisową nierzadko
trzeba sobie dokupić, ale o tym napiszemy więcej niebawem),
zawsze można skorzystać z usług wyspecjalizowanych firm.
I w praktyce różnica wobec opisanej powyżej sytuacji sprowadzi
się do tego, iż nasz plik wyślemy do zewnętrznej firmy, a
gotowy model przywiezie nam kurier…
Prawie jak z bajki...
Cyfrowe dane, wirtualny model, jak za dotknięciem
czarodziejskiej różdżki przybierają postać fizyczną. Otwieramy
magiczny „kuferek” stojący na biurku i wyciągamy z niego to,
co przed chwilą istniało jedynie w postaci zlepku bitów i
bajtów komputerowej informacji.
Wiele osób, mimo faktu, iż systemy „rapid prototyping” obecne
są już od ponad 10 lat (chociażby za sprawą stereolitografii,
opisywanej niegdyś na łamach miesięcznika CADCAM Forum –
wydania nr 5 i 11/99) na naszym rynku, traktuje je
podejrzliwie, jak jakąś „niepewną” nowość. Po co to? Na co? Do
czego może się przydać? I dlaczego takie drogie? Odpowiedzieć
na to ostatnie pytanie będzie łatwo po uzyskaniu odpowiedzi na
wcześniejsze. My nasz cykl zaczniemy jednak od odpowiedzi na
pytanie...
Jak
to działa?
Współczesne metody szybkiego prototypowania w przeważającej
większości zaliczane są do technologii przyrostowych
(addytywnych). Oznacza to, iż fizyczny model budowany jest od
podstaw, etap po etapie, warstwa po warstwie nakładanego w
określony sposób materiału. Oczywiście, prototyp możemy
uzyskać np. poprzez zamodelowanie jego kształtu chociażby w
glinie, stosując tutaj nie tylko metodę przyrostową (dodawanie
gliny), ale i ubytkową (jej usunięcie z wybranych miejsc), czy
też wykonując na tej podstawie formę – chociażby z piasku – i
wykonując odlew – nawet z metalu. Możemy także wyfrezować nasz
prototyp korzystając z centrum obróbczego sterowanego
numerycznie. Ale żadna z powyższych metod nie pozwoli nam na
wykonanie – w jednym przebiegu technologicznym – kompletnego,
działającego mechanizmu, składającego się np. z obudowy,
przekładni zębatej, przekładni łańcuchowej umieszczonej pod
dodatkową obudową. Modelu, w którym każde ogniwo łańcucha
będzie się ruszało, wykonane z precyzją determinowaną
jedynie... grubością warstw nakładanego materiału.
Systematyka
Metody szybkiego prototypowania możemy podzielić na wiele
rodzajów, jako kryterium przyjmując np. zastosowanie
uzyskanego modelu, sposób jego budowy, rodzaj i stan skupienia
materiałów użytych do jego budowy, czy też dokładność
wykonania. Kryterium zastosowania modelu możemy przyjąć jako
jedno z podstawowych, od niego bowiem będzie zależeć
technologia, jaką zdecydujemy się wykorzystać do jego budowy.
I
tak modele możemy podzielić na:
•
zapewniające jedynie wstępną weryfikację, czyli
odzwierciedlające kształt, formę modelu jedynie w sposób
przybliżony, mniej precyzyjny;
• funkcjonalne, czyli posiadające niektóre parametry zbliżone
lub nawet identyczne z parametrami właściwego wyrobu.
Pozwalają one na dokładną prezentację gotowego przyszłego
wyrobu, mogą posłużyć chociażby do oceny zainteresowania
produktem;
• będące w zasadzie gotowymi elementami. Są to modele wykonane
technologiami RP już jako seria próbna,
o wszystkich parametrach właściwego wyrobu. Możemy na nich
przeprowadzić badania własności fizycznych, przeanalizować
możliwość wprowadzenia zmian w już wytwarzanych produktach
etc.
Gdy
znamy zastosowanie naszego modelu, łatwo możemy określić, z
jakiego materiału powinien zostać wykonany i chociażby na tej
podstawie możemy dokonać wyboru technologii. A jest w czym
wybierać...
Stereolitografia (SLA)
Metoda ta (czy też – technologia) polega na punktowym
utwardzaniu ciekłego materiału (żywicy epoksydowej lub
akrylowej) przy użyciu wiązki laserowej małej mocy.
Naświetlona promieniowaniem ultrafioletowym żywica
foto-utwardzalna ulega polimeryzacji – utwardzeniu. Po
nałożeniu i utwardzeniu jednej warstwy (patrz ramka), proces
jest powtarzany dla kolejnej i tak aż do wyprodukowania całego
modelu. Jeżeli stopień skomplikowania konstrukcji tego wymaga,
budowane są także specjalne podpory podtrzymujące elementy
konstrukcji. Podpory są generowane automatycznie, przez
program sterujący procesem prototypowania, podczas konwersji
pliku zawierającego geometrię z systemu CAD. Po wyjęciu z
maszyny gotowego modelu, w przypadku stereolitografii zmuszeni
jesteśmy do mechanicznego, ręcznego usunięcia owych podpór.
Warto zwrócić uwagę na fakt, iż budowa modelu wiąże się z
zużyciem materiału nie tylko potrzebnego na zbudowanie jego
bryły, ale także – na wspomniane podpory. W innych
technologiach spotkamy się także z użyciem dwóch rodzajów
materiału – właściwego, służącego do budowy modelu, i
podporowego, o odmiennych właściwościach fizyko-chemicznych.
3D printing, czyli skąd wzięło się pojęcie „druku 3D”
„3D
printing”, czyli jak można by to określić: drukowanie
przestrzenne – jest kolejną technologią szybkiego
prototypowania. Opracowana została pod koniec lat
osiemdziesiątych w Massachusetts Institute of Technology
(Cambridge), znanym szerzej jako „MIT”. W zasadzie jest to,
obok stereolitografii, jedna z pierwszych (najstarszych) metod
szybkiego prototypowania; to w pewnym stopniu tłumaczy
popularność określenia „druk 3D” w stosunku do ogółu technik
RP.
W
technologii tej, budowa modelu polega na rozprowadzeniu
warstwy proszku na platformie maszyny i sklejeniu cząsteczek
odpowiednim spoiwem w miejscu odpowiadającym kształtowi
przekroju poprzecznego drukowanego w ten sposób elementu.
Grubości kolejno nakładanych warstw wahają się w granicach
0,01 – 0,2 mm, w zależności od stopnia dokładności
odwzorowania i skomplikowania drukowanego detalu. W tej
technologii można posłużyć się w zasadzie każdym materiałem,
który uda się sproszkować, a następnie spoić. W praktyce
największą trudność stanowi właśnie spojenie proszku.
Najczęściej stosowanym tworzywem są różne wariacje gipsu –
przemawia za tym łatwość spojenia, niski koszt i dostępność.
Stosowanym spoiwem jest w tym wypadku woda.
Piszący te słowa zdecydował się kiedyś na przeprowadzenie
małego eksperymentu. Wykorzystując „złom” drukarki
atramentowej HP (monochromatycznej), jej głowice drukujące i
mechanizm przesuwu zarówno głowicy, jak i kartki papieru (z
tym, że zamiast kartki za pomocą dźwigni i rolek przesuwana
była taca z gipsem), spróbowałem – zastępując tusz wodą –
dokonać wydruku prostego kształtu. Można powiedzieć, iż w
zasadzie eksperyment zakończył się powodzeniem, chociaż
przeprowadzony został bynajmniej nie pod kontrolą aplikacji
CAD, tylko... wektorowego Corela; obiektem druku był sześcian,
a każda z warstw drukowana była w osobnym przebiegu (nie
rozwiązałem sposobu automatycznego nakładania kolejnej warstwy
gipsu); piszę o tym, bo może zachęci to kogoś do eksperymentów
we własnym zakresie.
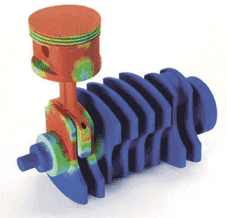
Wracając jednak do materiałów stosowanych w profesjonalnych
systemach druku 3D (tym razem bez cudzysłowu), oprócz gipsu,
stosuje się także wosk, celulozę, dekstran i ich mieszanki.
Wyroby wykonane z tych materiałów charakteryzują się małą
wytrzymałością. Stąd ich zastosowanie ogranicza się raczej do
budowy modeli i pokazowych prototypów. Możliwe jest jednak
wykorzystanie – w zbliżonej technologii – materiałów
metalicznych, ceramicznych. Konieczne jest wtedy zastosowanie
odpowiednich spoiw – koloidów.
Fused Deposition Modelling (FDM)
Znane w skrócie jako FDM, polega na budowaniu modelu poprzez
nakładanie kolejnych warstw półpłynnego, termoplastycznego
materiału, podawanego przez termiczne głowice wyposażone w
wymienne dysze. Gdy konieczne jest wykonanie elementu
podporowego, w kolejnej warstwie oprócz właściwego materiału
dokładany jest także materiał podporowy (z ang. support).
Charakterystyczne dla tej technologii jest to, iż oba rodzaje
materiału dostępne są w postaci włókien nawiniętych na bębny
umieszczane z tyłu maszyny (fot.). Włókna są odwijane i
podawane do głowicy, w niej podgrzewane do stanu półpłynnego i
nanoszone w postaci warstwy, która szybko stygnie i
twardnieje, tworząc podstawę dla kolejnych warstw. Głowice
drukujące poruszają się w osiach X-Y, natomiast podstawa
(stolik), na której budowany jest model, porusza się w osi Z –
opuszcza po nałożeniu każdej warstwy. Jak łatwo się domyśleć,
opuszcza o wartość odpowiadającą grubości nałożonej warstwy.
FDM
zostało opatentowane przez firmę Stratasys, obecną na naszym
rynku już od kilku lat. W maszynach do FDM możemy zastosować
różne rodzaje materiału, w tym także odpowiadające
właściwościami tworzywom stosowanym na co dzień w przemyśle
(np. ABS-M30, który jest o ponad 67% trwalszy niż standardowy
ABS!). Świadczy to o możliwościach zastosowania
modeli/prototypów uzyskanych w tej technologii także w
charakterze serii próbnej, lub jako pełnowartościowych
produktów małoseryjnych (nawiasem mówiąc, maszyny serii FDM
900mc w pewnym stopniu... „same się produkują”, tzn.
wytwarzają komponenty do budowy kolejnych egzemplarzy!
Prawie... perwersja!).
(...)
Pełna treść artykułu wraz
z ilustracjami w numerze (plik pdf) do pobrania z Archiwum
Źródła:
A.
Grochowiak: „Rapid prototyping i rapid tooling”, CADCAM Forum,
wydania: maj, czerwiec i lipiec 2000
M. Bubicz: „Raport: szybkie prototypowanie. Przegląd
dostępnych rozwiązań...”, Projektowanie i Konstrukcje
Inżynierskie, wyd. 4(07) kwiecień 2008
M. Bubicz: „Cyfrowe czy jednak fizyczne”, Projektowanie i
Konstrukcje Inżynierskie, wyd. 1(01) październik 2007
http://www.mit.edu/
http://home.utah.edu/~asn8200/rapid.html
www.bibusmenos.pl
www.prosolutions.com
www.z-corp.com
|
Blog monitorowany
przez:
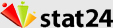 |