  .png)
W przygotowaniu
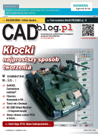
nr 5-6(25-26) 2017
dostępny
po 29.12.2017
Wydanie aktualne
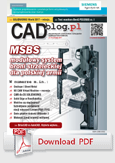
nr 3-4(23-24) 2017
dostępny w pdf, wydanie
flash
tutaj
Wydania
archiwalne
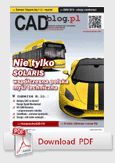
nr 1-2(21-22) 2017
dostępny w pdf, wydanie
flash
tutaj
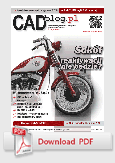
nr 1-2(19-20) 2015
dostępny w pdf, wydanie
flash
tutaj
2014_miniatur.png)
numer 1(18) 2014
dostępny w pdf, wydanie
flash
tutaj
2013_sm.png)
numer 1(17)
2013
dostępny w pdf, wydanie flash
tutaj
_covsmall.gif)
numer 1(16) 2012
dostępny
w
archiwum
2011_cover_small_ok.gif)
numer 1(15) 2011
dostępny
w
archiwum
cov_small.gif)
numer 4(14) 2010
HD dostępny
w archiwum
2010_cover_sma.gif)
numer 3(13) 2010
HD dostępny
w archiwum
2010small.gif)
numer 2(12) 2010
dostępny
w archiwum
2010_rgb_sm.gif)
numer 1(11) 2010 dostępny
w archiwum
2009_cover_web_small.jpg)
numer 9(10) 2009
już dostępny
w archiwum
_cover_web_small.jpg)
numer 8(9) 2009
już dostępny
w archiwum
|
Środa,
19.02.2014 r.
Współczesne systemy CAM
.png)
Wiele osób uważa, iż w całym
cyklu życia produktu to właśnie systemy CAM odgrywają kluczowe
znaczenie. Pod angielskim terminem Computer Aided
Manufacturing kryją się komputerowe systemy wspomagające
wytwarzanie, których głównym zadaniem jest integrowanie fazy
projektowania
i wytwarzania. To dzięki ich wykorzystaniu zamysł projektanta
i konstruktora przybiera
postać fizyczną, także wielkoseryjną...
Autor:
Maciej Stanisławski
Artykuł ukazał się na łamach
dwumiesięcznika STAL (wydania
9-10/2012, 11-12/2012 i 1-2/2013)
Rys. winietowy: DMG/MORI SEIKI
„Zastosowanie zaawansowanego systemu CAM (komputerowego
wspomagania wytwarzania) do sterowania maszyn CNC owocuje
skróceniem czasu programowania, wyeliminowaniem ryzyka
wystąpienia kolizji, obniżeniem kosztów i ostatecznie
zwiększeniem wydajności pracy zarówno ludzi, jak i urządzeń”.
Mniej więcej tego typu „opis wprowadzający” znajdziemy na
każdej stronie internetowej producenta bądź oferenta systemów
CAM – z tym, że w miejsce wielokropka należy wpisać nazwę
konkretnego systemu. Nie zmienia to faktu, iż powyższe
stwierdzenie w zasadzie w każdym przypadku jest prawdziwe.
Wszystkie współczesne systemy CAM,
nawet darmowy FreeMill, generują kod NC (dla obrabiarek
numerycznych) na podstawie modelu gotowego detalu. Model może
powstać albo wewnątrz systemu CAM, albo zostać zaimportowany z
systemu CAD. Nie ma znaczenia, czy dany detal ma postać
dokumentacji 2D, czy modelu 3D – w obu przypadkach na
podstawie danych geometrycznych system CAM pozwala na
uzyskanie kodu sterującego maszyną wytwórczą. Wydajny system
CAM oferuje szeroką gamę metod obróbki dla jednego detalu lub
rodzin części. Ustala wartości posuwów i obrotów na podstawie
zaimplementowanych (lub definiowanych przez użytkownika) baz
materiałów i narzędzi. Umożliwia także – przynajmniej w teorii
– wygenerowanie kodu na w zasadzie dowolny układ sterowania
obrabiarki numerycznej. W praktyce bowiem najczęściej
konieczne jest napisanie dedykowanego dla danej maszyny
postprocesora. To, czy odbędzie się to w środowisku systemu
CAM, czy też poza nim, stanowi także o jego wartości.
Aby zrozumieć znaczenie rozwiązań
stosowanych w najnowszych systemach CAM, warto przypomnieć
sobie istotę i sposób ich działania.
W początkach rozwoju techniki NC,
w zależności od technologiczności konstrukcji (patrz
ramka) części obrabianych, obrabiarki programowano
ręcznie, bądź maszynowo (ze wspomaganiem komputerowym). Ręczne
pisanie programów na maszyny obróbcze miało sens w przypadku
urządzeń pracujących w dwóch, maksymalnie trzech osiach.
Ciągły rozwój i doskonalenie maszyn i technik obróbczych, a
także szybki postęp w dziedzinie elektroniki, spowodował
opracowanie sterowania CNC połączonego magistralą danych z
komputerem nadrzędnym (komputer DNC, w literaturze fachowej
często nazywany serwerem plikowym, który przechowuje programy
NC, administruje nimi, przesyła do obrabiarki i kontroluje
pracę tego podsystemu).
Technologiczność konstrukcji
Jakże często
słychać głosy młodych konstruktorów mówiących o tym, iż CAM
pozostawiają inżynierom produkcji
i technologom i niech oni się z tym męczą. Liczy się projekt,
znakomity i zdumiewający model opracowany w CAD, wirtualny
prototyp będący odzwierciedleniem (nie urzeczywistnieniem)
koncepcji jego twórcy.
A jeśli... nie da się go wykonać? Na przykład z powodu braku
odpowiedniej technologii...
A przecież
technologiczność, jedna z istotnych szczegółowych zasad
konstrukcji, powinna w świadomości konstruktora obejmować nie
tylko etap wytworzenia danego detalu, ale także – jego
późniejszy serwis, czy też ewentualne naprawy (chociaż
współcześnie to ostatnie coraz częściej nie jest brane pod
uwagę – w interesie producenta klient powinien kupować nowy
produkt w miejsce zużytego, nie nadającego się już do naprawy,
lub którego naprawa nie będzie opłacalna – choćby ze względów
technologicznych). Ale nawet w przypadku produktów, maszyn i
urządzeń przeznaczonych do dłuższej eksploatacji bywa tak,
iż konstruktor uwzględnił jedynie technologię montażu...
Wraz z rozwojem oprogramowania
CAD, równolegle postępował rozwój systemów, mających na celu
integrację procesów projektowania i wytwarzania. Coraz
częściej w jednym środowisku programowym możliwe było
wykonanie nie tylko projektu danej części, ale także –
opracowanie strategii jej obróbki i wreszcie wygenerowanie
kodu sterującego obrabiarką. W wielu przypadkach doświadczony
projektant, który opanował także moduły, czy też podsystemy
CAM współpracujące ze środowiskiem jego oprogramowania CAD,
jest w stanie wykonać przynajmniej część pracy, która
wcześniej zarezerwowana była jedynie dla inżyniera produkcji
bądź technologa; może ona np. polegać na przygotowaniu takiej
wersji ostatecznej danego detalu, która nadawać się będzie do
wykorzystania jako model odlewniczy, uwzględni zachowanie
materiału podczas rozkroju detalu na arkuszu blachy itp. Nie
jest to jednak regułą i spotykane jest w zasadzie najczęściej
w małych przedsiębiorstwach...
Jak działa CAM
Budowa systemu CAM
jest podobna do CAD, jednak zamiast rozbudowanego modułu
modelowania, system ten zawiera moduł procesów. Nie znaczy to,
iż na rynku nie ma obecnych systemów CAM, które pozwalają na
zamodelowanie od podstaw detalu, który następnie ma zostać
poddany obróbce. W przypadku systemu CAM istotą jednak stała
się możliwość pracy z danymi o modelu zaimportowanymi z
systemów CAD, natomiast środowisko CAM powinno zapewniać
dostęp do informacji odnośnie maszyny, na której dany detal
powstanie, dostępnych narzędzi i przewidywanych parametrów
pracy. Ten sam detal może powstać na zaawansowanym centrum
obróbczym niemalże w jednym przebiegu maszyny, jak również na
kilku stanowiskach, na których obróbka – w zależności od
możliwości konkretnych obrabiarek – podzielona zostanie na
etapy.
Podstawę do opracowania programów
sterujących obrabiarkami NC stanowią dane geometrycznego opisu
modelu produktu (model CAD) i dane technologiczne – jak
chociażby wartości parametrów skrawania. Ale nie tylko.
Konieczne są także informacje na temat położenia obrabianego
obiektu w maszynie (w jej przestrzeni roboczej), położenia
narzędzia względem obiektu, wreszcie – wymiary obiektu na
poszczególnych etapach obróbki (materiał wyjściowy –
półprodukt – produkt gotowy). Dane związane z konstrukcją
zawarte są w modelu uzyskanym z systemu CAD. Natomiast dane
niezbędne do jego wytworzenia na konkretnym stanowisku
roboczym – przygotowane zostaną przez system CAM. Ale żeby
mogły powstać, CAM musi mieć dostęp do danych z programu
sterowania obrabiarką, do plików CLData pochodzących z
procesora NC urządzenia wytwórczego.
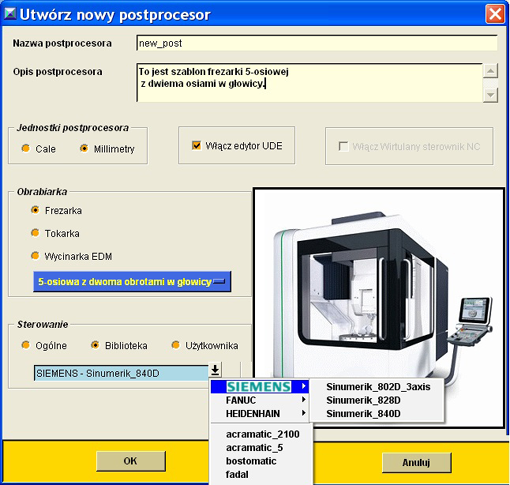
Środowisko
tworzenia postprocesorów w systemie CAM. Widoczne menu wyboru
sterowników maszyn NC
Źródło:
CAMdivision
Aby program obróbki uruchomić na
obrabiarce NC, należy najpierw z pliku CLData wygenerować
postprocesor, który dostosuje program do wewnętrznego języka
sterownika CNC, odpowiedniego dla danej maszyny. Postprocesor
NC jest programem tłumaczącym neutralny plik tekstowy CLData
na wewnętrzny język sterownika NC konkretnego producenta (tzw.
G-kod), innymi słowy – jest odpowiedzialny za wygenerowanie
kodu NC na odpowiednia maszynę z odpowiednim sterowaniem.
System CAM generuje „uniwersalną” ścieżkę narzędzia, a dopiero
postprocesor zamienia geometrie ścieżek z programu na linie
kodu NC „zrozumiałe” dla danej maszyny i jej sterownika.
System CAM dysponuje własnymi postprocesorami, ale nierzadko
pojawia się konieczność napisania „ręcznie” odpowiedniego dla
danej maszyny postprocesora.
CLData (z ang.
Cutter Location Data) to dane opisujące parametry obróbki i
przebieg trajektorii narzędzia w obróbce skrawaniem. To na ich
podstawie system CAM generuje odpowiednie instrukcje...
W zasadzie każdy współczesny
system CAM potrafi dobrać optymalne narzędzia i warunki pracy,
pod kątem detalu, który ma zostać wytworzony. Większość
wyposażona jest także w symulator, dzięki któremu użytkownik
może prześledzić cały proces obróbki na ekranie monitora oraz
sprawdzić, czy nie wystąpi przypadkiem kolizja narzędzia z
obrabianym detalem czy nawet wyposażeniem maszyny. Jeśli
wszystko jest w porządku, pozostaje wydać polecenie
automatycznego wygenerowania kodu sterującego obrabiarką.
Czy wiedza ta ma istotne
znaczenie z punktu widzenia użytkownika końcowego? Odpowiedź
jest prosta i brutalna: w zasadzie – nie ma. Dużo istotniejsza
w praktyce okazuje się przejrzystość interfejsu użytkownika,
integracja systemu z używanym środowiskiem programowym, a
także możliwość wykorzystywania wyspecjalizowanych modułów,
znacznie ułatwiających wykonanie określonego detalu w
dedykowanej dla niego technologii. A także – wspomniane
symulacje...
Symulacje i wirtualne maszyny
Automatyczne przejęcie wszystkich danych geometrycznych
potrzebnych do programowania NC jest obecnie realizowane w
większości systemów dostępnych na rynku. Najbardziej
zaawansowane „kombajny” CAD/CAM potrafią samodzielnie,
automatycznie generować dane technologiczne. Opis metodą figur
geometrycznych ułatwia sprawdzanie poprawności procesów
obróbki i manipulacji przedmiotu na drodze symulacji.
Symulacje te są szczególnie ważne w badaniach sytuacji
kolizyjnych zachodzących pomiędzy przedmiotem obrabianym,
narzędziem i urządzeniami mocującymi.
Dla ujawnienia sytuacji
kolizyjnych wybierane są, w trakcie przygotowania produkcji,
modele przestrzenne narzędzi i urządzeń mocujących (z
biblioteki modeli figur geometrycznych). Projektowana
komputerowo trajektorie ruchu narzędzia otacza się symulowaną
przestrzenią roboczą. Za pomocą wspomnianego algorytmu
przenikania figur geometrycznych kontrolowane jest
występowanie części wspólnych obrabianych brył, trajektorii
ruchu, elementów maszyny lub stanowiska roboczego, w tym
przede wszystkim modelu przestrzennego obrabianego przedmiotu,
osadzonego w jego zamocowaniu. Pojawienie się na którymś z
etapów części wspólnej jest równoważne wystąpieniu sytuacji
kolizyjnej.
Nie tylko producenci systemów CAM
zadbali o to, by użytkownicy ich oprogramowania mieli
możliwość „przećwiczenia” obróbki danego obiektu w wirtualnym
środowisku komputerowego systemu. Także producenci centrów
obróbczych wyszli naprzeciw temu zapotrzebowaniu, oferując
„wirtualne maszyny” – dokładne modele cyfrowe typoszeregów
produkowanych maszyn. Modele uwzględniające wszystkie
parametry rzeczywistych urządzeń (geometryczne, kinematyczne i
dynamiczne), a także sterowników, w jaki są one wyposażone (PLC,
CNC).
Na ekranie komputera użytkownik
widzi te same wymiary, charakterystykę, cykle i te same opcje,
jakie występują na rzeczywistej maszynie. Posuw, obciążenie
narzędzia, prędkość obrotowa wrzeciona czy podajnik narzędzia
jest dokładnie taki sam, jak w oryginale. Wszystkie kroki
symulacji są oparte na czasie cyklu i danych z rzeczywistej
maszyny. Dla przykładu, każdy krok, który jest testowany lub
zmieniany na wirtualnej maszynie, odzwierciedla rzeczywistą
sekwencję. Wirtualna maszyna wykorzystuje modele 3D podajników
narzędzi, wrzecion czy standardowych narzędzi. Narzędzia do
toczenia, frezowania, szlifowania są szczególnie ważne dla
symulacji. Tylko jeśli opis geometrii narzędzia jest kompletny
(zawierający rzeczywistą geometrię ostrza skrawającego,
korpusu narzędzia i płytki skrawającej) symulacja może być
właściwie przeprowadzona.
.png)
Przykład
symulacji procesu obróbki na podstawie wygenerowanego kodu NC.
Środowisko systemu NX CAM 7.5
Źródło:
CAMdivision
.png)
Symulacja
obróbki promienia podstawy łopatki. System NX CAM 7.5
Źródło:
CAMdivision
Wirtualne maszyny używają poleceń
składowych do implementacji programów NC sterujących
kolejnością ruchów rzeczywistej maszyny. Technologię tą firma
Siemens opracowała w 2004 roku, w ramach projektu badawczego
Integrated Virtual Product Development (iViP). I tak spotykane
w wirtualnych maszynach oprogramowanie Virtual NC Kernel(VNCK)
jest kopią jądra sterownika SINUMERIK 840D. Nawiasem mówiąc,
zaawansowane funkcje systemu SINUMERIK 840D można zastosować w
wielu różnych typach nowoczesnych wieloosiowych obrabiarek
wyposażonych w to sterowanie. Jeśli system CAM może generować
zoptymalizowany kod NC dla sterowania SINUMERIK, wówczas praca
takiej obrabiarki jest znacznie bardziej wydajna.
Prześledzenie procesu obróbki na
wirtualnym urządzeniu pozwala nie tylko na ostateczną
weryfikację zarówno modelu, którego technologiczność mogłaby w
skrajnym przypadku uniemożliwić jego wykonanie na prawdziwej
obrabiarce danego typu, ale także na całkowite
zoptymalizowanie procesu wytwórczego. Z pełną gwarancją
skuteczności i powodzenia całego przedsięwzięcia. Pod tym
względem może okazać się znacznie lepsze, niż symulacje, które
użytkownik znajdzie w systemie CAM.
.png)
Modele
opracowane w Tecnomatix RealNC służą do przedstawienia 3D
procesu obróbki na ekranie komputera. To oprogramowanie
uzupełnia geometrię maszyny i narzędzi o charakterystyki
ruchowe, które są dostarczane z modelu kinematycznego
zawierającego ponadto symulację usuwania materiału. Połączenie
RealNC i VNCK dostarcza bliską rzeczywistości symulację
wszystkich kroków procesu
Źródło:
Siemens PLM Software
Możliwości
współczesnych systemów CAM
Wyznacznikiem
współczesnego „standardu” wśród systemów CAM jest szereg
funkcjonalności dostępnych już w bazowym (tzn. pozbawionym
rozszerzeń i dodatkowych modułów) programie. Dla przykładu, w
przypadku wycinarek istotną funkcjonalnością będzie nesting –
pozwalający na automatyczne rozmieszczenie elementów na
arkuszu blachy (lub innego materiału). Co więcej, owo
rozmieszczenie dokonywane jest na podstawie algorytmów, które
pozwalają uzyskać optymalne wyniki.
Czym są
współczesne systemy CAM?
Termin CAM –
czyli komputerowe wspomaganie wytwarzania (ang. Computer Aided
Manufacturing) – obejmuje wszystkie etapy związane z procesem
wytwarzania. Należą do nich:
• tworzenie
harmonogramów prac,
• obróbka,
montaż,
• kontrola
jakości,
• organizacja
transportu międzyoperacyjnego.
Cechą
charakterystyczną systemów CAM jest transformacja
(przetwarzanie) obiektów (modeli) powstałych w wyniku
modelowania komputerowego 2D/3D na instrukcje maszynowe (na
kod CNC, sterujący pozycją narzędzia obróbczego), które
umożliwiają wytwarzanie elementów. Jak widać, ich
przeznaczenie jest zupełnie inne niż systemów CAD, faktem
natomiast pozostaje, iż swoje funkcje realizują często w
podobnym, lub wręcz identycznym (w przypadku zintegrowanych
systemów) środowisku (w obrębie jednej aplikacji, z
identycznym interfejsem etc.).
W przypadku kilku-osiowych maszyn
obróbczych, istotne znaczenie ma planowanie ścieżek obróbki, w
tym wstępne pozycjonowanie osi obrotowej, mające na celu m.in.
zapobieganie powstawaniu skaz (tzw. znaków) na uzyskanej
powierzchni, wywołanych zatrzymaniem pracy maszyny,
zapobieganie roboczym przejściom narzędzi.
Dzięki najnowszym algorytmom
generowania ścieżek narzędzia oraz innowacyjnym strategiom
obróbki, współczesne systemy CAM pozwalają na skrócenie czasu
obróbki o czterdzieści i więcej procent, w stosunku do
systemów poprzednich generacji. Towarzyszy temu także poprawa
jakości uzyskanej powierzchni, zwiększony zostaje – nawet
dziesięciokrotnie – czas życia narzędzia (tzw. „przebieg –
ilość obrabianych metrów”), wydłużona zostaje także żywotność
centrum obróbczego.
Obecne systemy CAM zawierają w
zasadzie wszystkie konwencjonalne strategie obróbki (obróbka
kieszeni, konturów, równoległa, promieniowa, spiralna), a w
wielu przypadkach również one zostały udoskonalone – łagodne
przejścia narzędzia (optymalizacja ścieżek i posuwów)
zmniejszają obciążenia, jakim ulega obrabiarka, a to przekłada
się na zdecydowanie lepszą jakość obrobionej powierzchni.
Kontrola obciążenia i posuw
Współczesne systemy
CAM udostępniają użytkownikom specjalne funkcje, pozwalające
na kontrolę wartości obciążenia narzędzia i wykrywają ścieżki
o dużym obciążeniu frezu. Wtedy stosują dla nich mniejsze
wartości posuwu. Optymalizacja szybkości posuwu automatycznie
analizuje obciążenia narzędzia wzdłuż ścieżki i dostosowuje
wartość posuwu dla zapewnienia równej ilości usuwanego
materiału, zwiększając w ten sposób żywotność narzędzia.
.png)
Wartości
obciążenia narzędzia i optymalizacja posuwu
Źródło:
CAMdivision
Wirniki w pięciu osiach
Najnowsze systemy
turbin oferują wysoką sprawność w wielu dziedzinach – od
generowania energii po silniki samolotowe. Jest to jedna z
przyczyn rosnącego zapotrzebowania na komponenty zawierające
elementy typu łopatki, które są najważniejszymi elementami
silników turbinowych. W ciągu ostatniej dekady nastąpiło
odejście od wytwarzania tarcz wirników turbin lotniczych w
postaci zestawów oddzielnych łopatek składanych z piastami na
rzecz produkcji pojedynczych komponentów. Już w samej historii
lotnictwa tego typu technologia wytwarzania owych narażonych
na wyjątkowe obciążenia zespołów stała się przyczyną wielu
wypadków i katastrof lotniczych (jak chociażby pamiętna
katastrofa w Lesie Kabackim samolotu Polskich Linii Lotniczych
LOT IŁ-62M, w którym na skutek oderwania się łopatek turbiny
doszło do uszkodzenia przewodów sterowania hydraulicznego i
pożaru). Jednorodna, pojedyncza część eliminuje w zasadzie
ryzyko powstania tego typu awarii, pod jednym wszakże
warunkiem – iż zostanie bezbłędnie zaprojektowana i wykonana.
Obróbka maszynowa wirników z
wieloma łopatkami wiąże się jednak z dodatkowymi wymaganiami w
zakresie programowania NC, które jest niezbędne w przypadku
obsługi obrabiarek wieloosiowych używanych do produkcji takich
elementów. Wielu dostawców systemów CAM wybiera takie
skomplikowane komponenty w celu potwierdzenia możliwości
oprogramowania w dziedzinie obróbki 5-osiowej, ale faktycznym
testem dla nich powinna być... produktywność programowania.
Niestety, w praktyce nierzadko okazuje się, że standardowe
oprogramowanie 5-osiowe nie spełnia wymogów wielozadaniowości
w tym zakresie. Dlatego podejmując decyzję o wyborze systemu
CAM, należy upewnić się, czy oferuje ono obsługę specjalnych
operacji zaprojektowanych z myślą o wydajnym programowaniu
ścieżek NC dla komponentów turbin.
Jeszcze przed paroma laty
specjalistyczne zadania dotyczące programowania i obróbki
maszynowej bardziej złożonych komponentów łopatek turbin i
wirników były realizowane przy użyciu zaawansowanych narzędzi
i specjalistycznego oprogramowania NC, dostarczanego wraz z
obrabiarką (sic!) lub kupowanego oddzielnie od
wyspecjalizowanego dostawcy. O tym, że możliwe będzie
projektowanie ścieżek dla takich komponentów bezpośrednio z
poziomu CAM, użytkownik mógł w zasadzie jedynie pomarzyć, albo
„eksperymentować”. Koszty takich eksperymentów mogły jednak
okazać się wysokie – wielokrotnie wyższe niż zakup
wspomnianego wyspecjalizowanego oprogramowania.
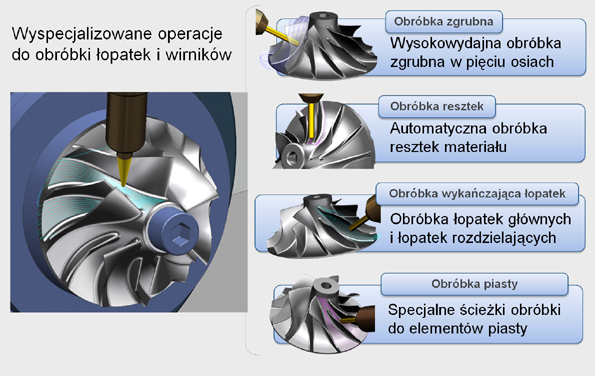
Rys.
powyżej: Typowe operacje obróbki (na przykładzie typowej, ale
sprawiającej wiele problemów części)...
Także sam zakup dodatkowych
aplikacji, czy narzędzi systemowych, nie zawsze sprawdzał się
w praktyce; lepiej jest przecież stosować oprogramowanie w
pełni zintegrowane z pozostałymi obszarami działalności. Poza
koniecznością obsługi rozwiązań wielu producentów oraz
przesyłania lub translacji danych, problem dotyczy również
zarządzania danymi i kontroli wersji. W przypadku większych
przedsiębiorstw problem polega na tym, że odrębne aplikacje
działają poza systemem zarządzania danymi produktów (PDM), co
powoduje wzrost kosztów związanych ze skutecznym
administrowaniem takimi informacjami. Ponadto – jak
wspomniałem – unikatowe, specjalistyczne pakiety
oprogramowania i ich aktualizacje najczęściej są bardzo
kosztowne.
Rozwiązaniem optymalnym z punktu
widzenia zarówno dostawców systemów CAM, jak i ich końcowych
użytkowników, okazały się dodatkowe funkcjonalności, lub też
moduły, maksymalnie ułatwiające programowanie skomplikowanych
części. Po przeprowadzeniu procesu instalacji, stają się one
integralną częścią używanych systemów CAM. Wiele wskazuje na
to, iż jednym z kierunków rozwoju współczesnych systemów CAM
będzie właśnie implementacja takich rozwiązań już do
standardowych, bazowych wersji programów.
Dobrym przykładem może być moduł
NX Turbomachinery, którego celem jest właśnie maksymalne
ułatwienie projektowania skomplikowanych części – elementów
wirników i turbin. System oferuje użytkownikom specjalizowane
operacje związane z programowaniem elementów urządzeń/silników
turbinowych.
Ideą jest proste wybranie
geometrii i wskazanie systemowi odpowiednich typów i elementów
łopatek w danej operacji. Po definicji parametrów
technologicznych operacji otrzymujemy całkowicie bezkolizyjne
ścieżki narzędzia dla całego komponentu, bez konieczności
wprowadzania do nich dalszych modyfikacji.
W przypadku braku specjalizowanych operacji w systemie CAM,
wygenerowanie ścieżki narzędzia tylko między dwiema łopatkami
i rozdzielaczem jest dużo bardziej czasochłonne.
Etapy
procesu wprowadzenia części do produkcji:
•
przygotowanie/edycja danych CAD;
• programowanie NC, a w nim:
– wybór strategii obróbki,
– określenie parametrów,
– wybór narzędzia,
– wybór sterowania/obrabiarki,
• postprocessing,
• walidacja programu.
Niektóre systemy CAM pozwalają
użytkownikom na zaprogramowanie wysokowydajnej obróbki
zgrubnej, podczas której można ograniczyć ilość zdejmowanego
materiału. Ma to istotne znaczenie w przypadku tak
wymagającego detalu, jak łopatka wirnika. Jest ona zazwyczaj
długa, a to może powodować odchylenie obrabianej części.
Zjawisku temu może zapobiec pozostawienie odpowiedniej masy
materiału, która usztywni obrabiany detal i w ten sposób
zminimalizuje odchylenie spowodowane obróbką skrawaniem.
Zaawansowany CAM umożliwia przeprowadzanie wysokowydajnej
5-osiowej obróbki zgrubnej (bez konieczności stosowania
pomocniczych powierzchni kontrolnych) poprzez określenie
takich parametrów, jak wzór ścieżki, punkt startu narzędzia,
odległości pomiędzy poziomami obróbki, głębokość obróbki,
szerokość skrawania, liczba przejść pomiędzy łopatkami,
odchylenie osi narzędzia oraz opcje wygładzania i wydłużania
ścieżek podczas obróbki krawędzi natarcia i spływu.
Reasumując: co powinno cechować
współczesny system CAM? Wymieńmy te najistotniejsze elementy:
• obsługa głowic obrotowych dla centrów obróbczych 5-cio
osiowych, współpraca z wieloosiowymi centrami obróbczymi (do
15 osi),
• interpolacja położenia biegunów i obsługa emulacji
frezarko-tokarek i frezarek,
• optymalizacja pozycjonowania osi obrotowej, zapobiegająca
roboczym przejściom osi liniowej,
• automatyczne przełączanie pomiędzy układami współrzędnych (xyz
i zxc), stanowiące dodatkową ochronę przed roboczymi
przejściami osi liniowej,
• optymalizacja ścieżek programów obróbczych w celu
zwiększenia żywotności narzędzia,
• możliwości obróbki High Speed Machining,
• trzypunktowa linearyzacja liniowa,
• automatyczne przekształcenie krzywych NURBS, Beziera i
krzywych Spline,
• dopasowanie krzywych,
• zaawansowany algorytm linearyzacji,
• generowanie cykli wiercenia, gwintowania, wytaczania,
• wykrywanie granic ruchu narzędzia,
• trzyosiowa kompensacja narzędzia,
• automatyczna kontrola obrotów wrzeciona i posuwu,
• dokładna kalkulacja czasu obróbki,
• pełna interpolacja liniowa, kołowa i heliakalna,
• kontrola automatycznej wymiany narzędzi,
• wspomaganie przechwytu przedmiotu przy obrabiarkach
wielowrzecionowych.
Powyższe wymagania spełnia w
zasadzie większość systemów dostępnych na rynku. Niektóre z
nich oferują także wyspecjalizowane moduły, stanowiące
wsparcie dla systemów CAD, istotne przy projektowaniu form
wtryskowych, tłoczników, narzędzi niezbędnych do udoskonalania
procesu produkcji. Natomiast osobnym zagadnieniem pozostaje
wymiana danych.
Synchronicznie w CAM? Dlaczego
nie...
Głównym problemem
występującym na styku systemów CAD i CAM jest wymiana danych
pomiędzy różnymi strukturami i modułami obu systemów.
Czynnikiem komplikującym jest fakt, że składniki sprzętowe i
programowe systemów CAD i CAM potrafią się znacznie od siebie
różnić. Pierwszy protokół interfejsu CAD/CAM opisany został w
amerykańskiej normie ANSI Y14.26M już w 1981 r. Określał on
właściwości interfejsu IGES (ang. Initial Graphics Exchange
Specification), przeznaczonego głównie do przesyłania rysunków
detali związanych z budową maszyn, opisywanych prostymi
modelami krawędziowymi i płaszczyznowymi. Przy przenoszeniu
danych detalu konstrukcyjnego z jednego do drugiego systemu
CAD/CAM, IGES zapewnia przetworzenie danych przez preprocesor
do formatu IGES w systemie wysyłającym i odtworzenie z danych
w formacie IGES postaci zapisu rysunku zrozumiałej dla tego
systemu, za pomocą postprocesora systemu przyjmującego.
Ponieważ każdy system CAD/CAM może być zarówno systemem
wysyłającym, jak i przyjmującym dane w formacie IGES,
niezbędne są w takim systemie preprocesor i postprocesor. Dane
IGES mają budowę sekwencyjną, korzystają z zestawu znaków
ASCII i używają 80 znakowego formatu rozkazów. Poważnym
ograniczeniem jest fakt, iż IGES nie jest w stanie przetwarzać
opisu opartego na figurach geometrycznych. Z tego powodu
Verband der Deutschen Automobilhersteller (niem. Związek
Niemieckich Producentów Samochodów) zaproponował nowy protokół
interfejsu międzysystemowego, nazywanego interfejsem
powierzchniowym VDA. Ten interfejs umożliwia przetwarzanie
nieanalitycznych danych nie posiadających opisu matematycznego
– są to przede wszystkim krzywe i powierzchnie o dowolnych
kształtach elementów karoserii samochodowych, matryc i
kształtowych elektrod erozyjnych. Innym systemem (i formatem
danych) uznanym za jeden ze standardów w dziedzinie CAM stał
się STEP (z ang. Standard for the Exchange of Product Modeling
Data).
Szczególne
zasady konstrukcji:
• funkcjonalność,
• niezawodność i trwałość,
• sprawność,
• lekkość,
• taniość i dostępność materiałów,
• właściwy układ przenoszenia obciążeń,
• technologiczność,
• łatwość eksploatacji,
• ergonomiczność,
• zgodność z obowiązującymi normami i przepisami.
A przecież potencjalne źródło
problemów może tkwić już w samej importowanej do systemu CAM
geometrii. I zamiana na format „uniwersalny”, jak STEP czy
IGES, nie oznacza, iż podczas konwersji z natywnego formatu
CAD-owskiego wszelkie błędy zostaną wyeliminowane – wręcz
przeciwnie. Modele idealnie wyglądające „z zewnątrz”, mogą
okazać się bardzo chaotyczne pod względem matematycznym;
typowe błędy powodujące odrzucenie modelu przez system CAM
(lub co gorsze – jego błędną interpretację) to niepełne
powierzchnie lub mikroskopijne (matematyczne) szczeliny między
powierzchniami danego detalu. To już wystarczy, by pojawiły
się błędy w obróbce całości. Programiści NC mogą być w takiej
sytuacji zmuszeni do skorygowania geometrii powierzchni lub
poprawienia jej definicji, ingerując w wyjściowy model,
oczywiście pozostawiając jego niezmieniony kształt. Chociaż w
pewnym zakresie także kształt wyjściowego modelu musi – ze
względów technologicznych – ulec nierzadko dodatkowym
modyfikacjom. Przykładem może być np. konieczność zaślepienia
otworów w modelu, w celu uzyskania jednorodnej i gładkiej
powierzchni na potrzeby obróbki wykańczającej, gdyż rzeczone
otwory zostaną wywiercone dopiero... po zakończeniu tego etapu
obróbki całego detalu.
.png)
Typowe
problemy z danymi pochodzącymi z systemów CAD, z jakimi muszą
radzić sobie użytkownicy systemów CAM,
inżynierowie produkcji, technolodzy...
Regułą jest także, iż projektanci
CAD dostarczają działom produkcji ostateczne wersje modeli
części, które wymagają wielu zmian, zanim zostaną wykorzystane
np. jako modele odlewnicze (zaprojektowanie odpowiednich
naddatków, pogrubienie ożebrowań, czy wspomniane już
zaślepienie otworów).
Spotykamy także wiele sytuacji, w
których przydaje się możliwość tworzenia specjalnych obiektów
na bazie podstawowej geometrii części. Typowe przykłady to
szczęki uchwytów tokarskich, czy niestandardowe elementy
mocowania. Wspomniana koncepcja modelu odlewniczego jest nieco
podobna do modelu bazowego półfabrykatu. Wszystkie powyższe
przykłady ilustrują sytuacje, w których inżynier produkcji lub
programista NC muszą wprowadzić odpowiednie modyfikacje do
źródłowego modelu części.
A wprowadzanie nagłych,
konkretnych zmian w projekcie? Po rozpoczęciu programowania NC
znacznie łatwiej jest wprowadzić modyfikacje do istniejącego
modelu bazowego 3D z poziomu środowiska CAM, niż zacząć pracę
od początku z nowym plikiem dostarczonym przez projektanta.
Gdy w 2008 r. Siemens PLM
Software wprowadził technologię projektowania synchronicznego
(Synchronous Technology), od razu zwrócono uwagę na
możliwości, jakie stwarza w kwestii szybkiego i łatwego
edytowania modeli. Technologii tej poświęcono wiele miejsca
już w osobnych opracowaniach, tutaj jedynie przypomnę, iż
pozwala ona na modyfikowanie modeli niezależnie od historii
ich projektowania. Zastosowano w niej nieznany dotąd poziom
„inteligencji”, dzięki czemu użytkownicy mogą zmieniać nawet
bardzo skomplikowane geometrie trójwymiarowe. Technologia
doskonale współpracuje z podstawowymi, „nie-inteligentnymi”
kształtami, które często powstają w wyniku translacji danych –
np. na formaty STEP lub IGES. Można ją nawet stosować do
trójwymiarowych modeli o nienaruszonej, aktywnej historii
projektowania (np. zaawansowanych modeli parametrycznych), nie
powodując żadnego jej uszkodzenia! To doskonała opcja z punktu
widzenia inżynierów produkcji, którzy nie są autorami części i
nie znają wszystkich szczegółów jej konstrukcji. Mimo
zachowania pierwotnej historii zmiany modelu są dokładnie
rejestrowane i dostępne do wglądu, czyli technologia ta
spełnia wymagania dotyczące kontroli procesów w środowisku
produkcyjnym.
W wielu przypadkach wiązań
geometrycznych (typu styczność, współosiowość, relacje
poziom/pion) absolutnie nie wolno „zrywać”. Synchronous
Technology rozpoznaje istnienie tych warunków i zachowuje je
podczas edycji, nawet jeśli nigdy nie zostały jednoznacznie
zdefiniowane lub utracono je w wyniku translacji. To bardzo
ważna funkcjonalność, szczególnie przy wprowadzaniu zmian w
systemie CAM (należy jednak pamiętać o konieczności
przestrzegania reguł zdefiniowanych w systemie CAD). W efekcie
jednym poleceniem można identyfikować i dopasowywać
sąsiadujące elementy geometrii (a nawet połączone z sobą
przekroje modelu) oraz wprowadzać do nich odpowiednie korekty.
Programista NC nie musi już wybierać między mniejszym, a
większym złem – próbą dostosowania parametrów pominiętych
przez projektanta albo modyfikacją poszczególnych elementów
geometrii za pomocą metod edytowania modelu podstawowego. Oba
podejścia mają swoje (opisane powyżej) wady, a projektowanie
modelu od początku może potrwać wiele godzin, a nawet dni.
Dzięki technologii synchronicznej
programista NC może w trójwymiarowym modelu wprowadzać zmiany,
jakich dotąd nie mógł dokonywać nawet zaawansowany użytkownik
systemu CAD, bez umieszczenia w modelu analogicznych
mechanizmów zmienności od samego początku.
CAM za free...
W odróżnieniu od
systemów CAD, praktycznie nie spotyka się rozwiązań CAM
oferowanych za darmo. Przyczyna wydaje się tylko jedna:
stopień zaawansowania i skomplikowania rozwiązań klasy CAM w
zasadzie wyklucza jakąkolwiek celowość udostępniania takich
rozwiązań bezpłatnie przez producentów, którzy utrzymują się i
inwestują w rozwój swoich systemów poprzez oferowanie ich za
odpowiednim wynagrodzeniem. Z kolei różne stowarzyszenia i
grupy entuzjastów, tworzących darmowe aplikacje oparte np. o
kod otwarty, rzadko dysponują wystarczającą wiedzą w
dziedzinie technik wytwórczych i technologii, aby zaoferować
rozwiązanie klasy CAM. Trzeba także wziąć pod uwagę, że użycie
darmowego systemu CAD, nawet w przypadku wystąpienia błędów w
działaniu programu, które przełożą się na niedoskonałość
projektu, nie spowoduje wysokich strat – najdroższy okaże się
czas poświęcony na pracę nad projektem i ewentualny przestój.
Natomiast niesprawdzone rozwiązanie CAM w skrajnym przypadku
może doprowadzić nie tylko do zmarnowania materiału, ale także
do uszkodzenia narzędzia, czy wręcz maszyny obróbczej.
.png)
Przygotowanie części do obróbki na maszynie 3-osiowej.
Środowisko darmowego systemu CAM – FreeMill
.png)
Przygotowanie narzędzia skrawającego. FreeMill jest
ograniczoną funkcjonalnie wersją systemu VisualCAM. Producent
nie zapewnia żadnego wsparcia, ale w sieci jest sporo
literatury, działa także forum użytkowników. Ale darmowe
rozwiązania CAM raczej nie mają przyszłości...
(...) Jedno wydaje się natomiast
pewne: czynnikiem decydującym o wyborze rozwiązania CAM na
pewno nie może być cena tego ostatniego.
(ms)
Źródła:
1. Anna Korcz: Komputerowe wspomaganie procesów wytwarzania
CAM. Scientific Bulletin of Chełm. Section of Mathematic and
Computer Science, nr 1/2009
2. Krzysztof Augustyn: NX CAM – nowe możliwości. CADblog.pl,
nr 2(12)2010
3. Krzysztof Augustyn: NX & Turbo Machinery. CADblog.pl, nr
3(13)2010
4. Aleksandra Jóźwiak: Ścieżki z Synchronous Technology.
CADblog.pl nr 2(12)2010
5.
http://camdivision.pl/pdf_strona/publikacje/podreczniki/VoluMill_NX_Guide.pdf
6. materiały prasowe producentów i resellerów systemów CAM
Artykuł ukazał się na łamach
dwumiesięcznika STAL (wydania
9-10/2012, 11-12/2012 i 1-2/2013).
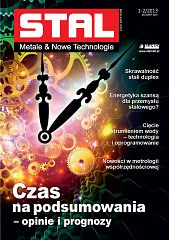
Polecane strony związane z
tematyką CAM i pokrewną...
www.cnc.info.pl
www.camdivision.pl
www.nxcad.pl
www.mecsoft.com
www.alphacam.pl
www.dmgmoriseikiusa.com
www.plm.automation.siemens.com
http://hypermill.pl/
http://www.automatyka.siemens.pl/
|
Blog monitorowany
przez:
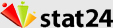 |